Fuel management is a critical component in the operation of any vehicle or industrial system dependent on petroleum-based products. A fuel level sensor (FLS), such as those provided by My GPS, offers real-time and accurate monitoring of the fuel column’s height within the tank, ensuring optimal fuel usage, preventing wastage, and detecting theft. This guide provides an in-depth look at fuel level sensors, including their types, operating principles, advantages, and specific applications in various industries.
The Importance of Fuel Level Sensors
Fuel level sensors are integral for any fleet or equipment manager who needs precise data on fuel usage. From maintaining a stable budget to preventing unauthorized fuel siphoning, FLS units deliver detailed insights into fuel status, helping businesses streamline operations. Below are some of the main reasons fuel level sensors have become essential:
Cost Control
By tracking real-time fuel usage, companies can minimize unnecessary fuel consumption, helping reduce overall operational costs.
Enhanced Security
FLS provides an additional layer of security by detecting fuel drains, making it easier to identify unauthorized fuel use and respond quickly.
Operational Transparency
FLS units are often integrated with GPS and telematics systems, giving managers access to detailed fuel reports that help them make informed decisions about fuel usage.
Fleet Efficiency
For logistics and public transportation fleets, real-time fuel monitoring helps prevent delays and ensures vehicles have enough fuel to complete their routes without interruption.
Quality Control in Refueling
Sensors can detect fuel levels during refueling, ensuring vehicles are refueled accurately and helping prevent engine malfunctions due to poor fuel quality or contaminants.
Types of Fuel Level Sensors
Fuel level sensors are available in different types, each with unique properties and advantages, making them suitable for various applications. The most commonly used FLS types include float, capacitive, and ultrasonic sensors. Each has distinct operational principles that provide varying levels of accuracy, reliability, and ease of integration with other systems.
1. Float Sensor
Description and Functionality: Float sensors are typically factory-installed in vehicles and use a float connected to a variable resistor. As the fuel level changes, the float moves, altering the resistance of the potentiometer. This change in resistance modifies the voltage, which is then displayed as an approximate fuel level on the vehicle’s dashboard.
Advantages
🡪Affordability: The float sensor is cost-effective and widely used in standard passenger vehicles.
🡪Ease of Use: Float sensors require minimal maintenance and are generally reliable for approximate fuel readings.
Limitations
🡪Accuracy: These sensors are only suitable for general fuel level indications and can have a margin of error between 10-30%, making them less ideal for applications requiring precise data.
🡪Limited Security: Because float sensors only display approximate fuel levels, they lack the capability to detect or prevent fuel theft.
2. Capacitive Sensor
Description and Functionality: A capacitive sensor is often added by the vehicle owner to improve accuracy and security. Capacitive sensors consist of two electrically isolated tubes that serve as electrodes. Fuel, acting as a dielectric, fills the space between these tubes. When the fuel level changes, so does the sensor’s capacitance, allowing it to calculate fuel volume with high precision.
Advantages
🡪High Accuracy: Capacitive sensors offer an impressive accuracy margin within 1-2%, making them suitable for businesses that require precise fuel usage data.
🡪Anti-Theft Capabilities: With accurate fuel monitoring, capacitive sensors can detect unusual fuel drainage and deter fuel theft.
🡪Versatility: These sensors work well in various conditions, including for trucks, agricultural equipment, and stationary fuel tanks.
Limitations
🡪Installation Complexity: Capacitive sensors may require professional installation to ensure they work optimally.
🡪Higher Cost: These sensors tend to be more expensive than standard float sensors due to their advanced design and high accuracy.
3. Ultrasonic Sensor
Description and Functionality: Ultrasonic sensors are placed outside the fuel tank, typically at the bottom, and emit sound waves that travel through the fuel layer. The sensor calculates fuel levels based on the reflection time of the ultrasonic waves, providing a non-contact measurement that avoids contamination or degradation.
Advantages
🡪Non-Contact Measurement: Because the sensor operates externally, there is no risk of contact with fuel, reducing wear and maintenance.
🡪Exceptional Accuracy: With proper calibration, ultrasonic sensors provide highly accurate fuel measurements.
🡪Integration with Telematics: Ultrasonic sensors can be connected to GPS tracking systems, giving operators real-time insights into fuel usage.
Limitations
🡪Environmental Sensitivity: The performance of ultrasonic sensors can be influenced by factors such as temperature and humidity.
🡪Initial Calibration Required: To ensure accuracy, the tank must be calibrated with a reference table, a process that can take time.
Applications of Fuel Level Sensors in Various Industries
Fuel level sensors have significant applications across diverse industries, enabling better control over fuel consumption, reducing costs, and preventing theft.
1. Transportation Industry
Fuel level sensors are essential in the transportation industry, where fuel consumption significantly impacts overall costs and efficiency. Applications include:
🡪Commercial Cargo Transport: Sensors assist logistics managers in planning fuel stops based on accurate fuel data, reducing downtime and ensuring timely deliveries.
🡪Passenger Transport: In public transportation, FLS units help prevent fuel shortages, ensuring buses, taxis, and other passenger vehicles maintain uninterrupted operation.
🡪Agricultural Machinery: Fuel level sensors monitor fuel levels in tractors, harvesters, and other equipment, helping operators manage fuel resources effectively across large farming areas.
2. Industrial and Storage Applications
Fuel level sensors are widely used in the industrial sector for fuel storage and management, particularly where large volumes of fuel or other liquid hydrocarbons are stored.
🡪Fuel Storage Tanks: FLS units are commonly installed in aboveground and underground tanks at gas stations to track fuel levels accurately.
🡪Railway Transport: Fuel level sensors monitor fuel levels in rail tankers, providing real-time data on fuel levels during long-distance travel, which helps logistics companies optimize fuel usage.
3. Marine Industry
In marine applications, fuel level sensors provide reliable data on fuel reserves for boats, yachts, and commercial vessels. This real-time data is essential for navigation planning, especially on long journeys where refueling stations are few and far between.
4. Construction Equipment
Construction equipment, such as cranes, excavators, and loaders, operates in remote locations where fuel monitoring is crucial to avoid downtime. Fuel level sensors installed in construction machinery help reduce operational delays by ensuring timely refueling and monitoring fuel theft in high-risk areas.
Operating Principles of Fuel Level Sensors
Fuel level sensors operate using various mechanisms based on their type. Here is an overview of their working principles:
🡪Float Sensor
The float sensor uses a mechanical float attached to a potentiometer, which changes resistance as the float moves up or down with the fuel level.
🡪Capacitive Sensor
This sensor type measures capacitance, which changes based on the amount of fuel acting as a dielectric between two electrodes. The sensor calculates the fuel level based on these capacitance changes.
🡪Ultrasonic Sensor
The ultrasonic sensor calculates fuel levels by emitting sound waves through the fuel tank. The sensor detects the time difference between sending the ultrasonic signal and receiving its reflection, which correlates to the fuel level.
Installation and Configuration of Fuel Level Sensors
Installing a fuel level sensor involves careful planning and professional handling to ensure accuracy and adherence to safety regulations.
Installation Steps
- Identify the Installation Point: Choose a location within the fuel tank or in proximity for external sensors, ensuring easy access for maintenance.
- Install the Sensor: Secure the sensor in place, either inside the tank (for capacitive and float sensors) or outside the tank bottom (for ultrasonic sensors).
- Connect to the Vehicle’s Electrical Network: Connect sensor wires to the vehicle’s network or GPS tracker, generally near the dashboard or under the hood.
- Sensor Configuration: Set thresholds for low-fuel alerts and calibrate the sensor to ensure accuracy.
- Operational Testing: Fill the tank and compare the readings to actual fuel levels to verify the sensor’s functionality.
It’s recommended to have sensors installed by professionals, especially in vehicles or storage tanks, to comply with safety regulations.
Selecting Fuel Level Sensors with My GPS in Dubai
My GPS in Dubai offers fuel level sensors designed for vehicles, industrial storage, and fleet management. Their sensors can be integrated with GPS systems, enabling managers to monitor fuel levels in real-time, track fuel usage, and protect against theft. With options to monitor additional metrics like temperature and vehicle condition, My GPS sensors are comprehensive tools for fuel management and operational efficiency.
Conclusion
Fuel level sensors provide essential data that enhances vehicle management, prevents theft, and optimizes fuel consumption. With various types available – from float and capacitive to ultrasonic sensors – businesses can choose a solution that meets their specific needs. Proper installation and integration of these sensors ensure that fuel usage is efficient, secure, and cost-effective, making fuel level sensors a wise investment across industries such as transportation, construction, and fuel storage. As technology advances, FLS systems will continue to play a critical role in promoting sustainable fuel use and operational transparency.
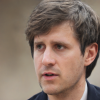
Skydiver, feminist, band member, Mad Men fan and holistic designer. Acting at the crossroads of modernism and intellectual purity to craft delightful brand experiences. Let’s design a world that’s thoughtful, considered and aesthetically pleasing.
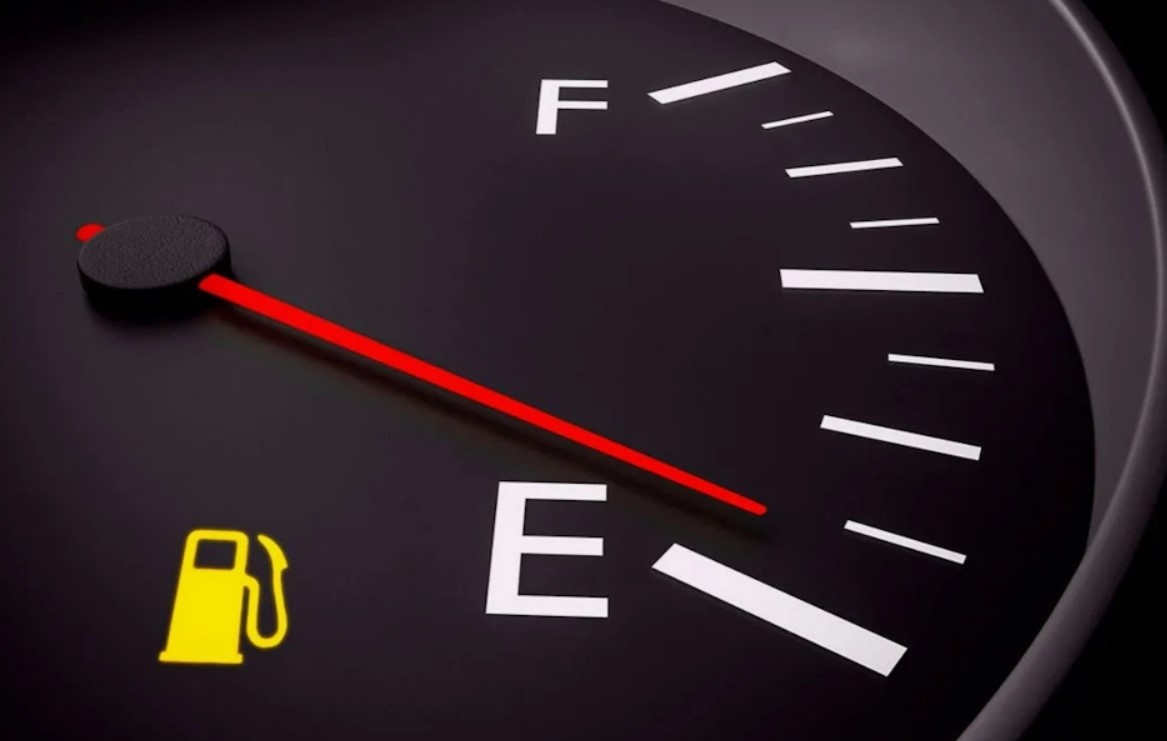